At Zwicker Kugellager GmbH, you can obtain everything to do with special ball bearings — such as deep groove ball bearings with special greasing, ceramic balls, hard material and other special cages as well as matched bearing pairs. As a manufacturing company, Zwicker Kugellager GmbH has found a reliable and fast partner in Spanflug for ordering its CNC parts
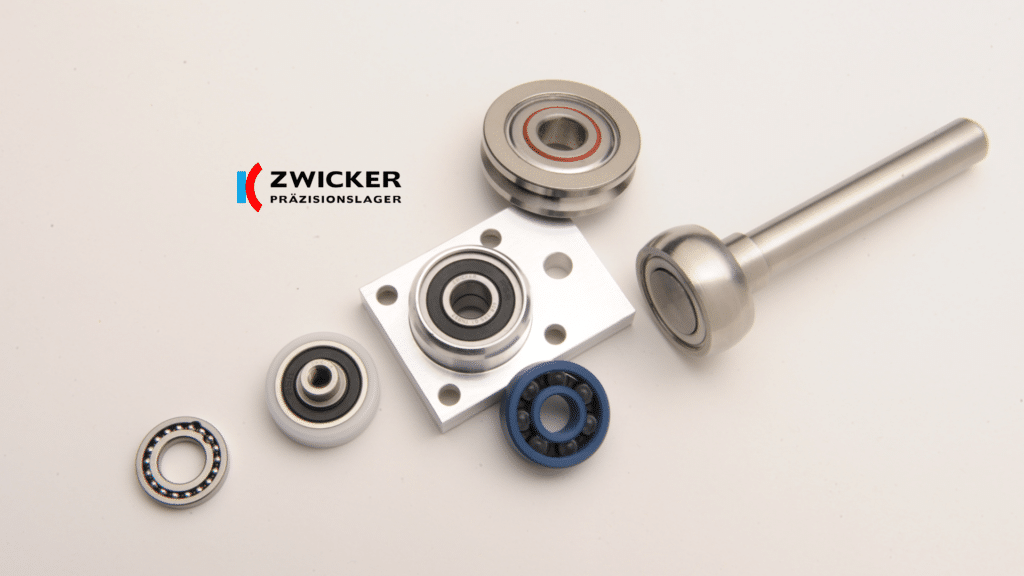
Carola Zwicker
Management,
Zwicker Kugellager GmbH, a company of the KÜNEMUND GROUP
What are the ordered parts used for?
The parts requested and ordered from Spanflug are used for special ball bearings or assemblies with bearings. The parts are mostly made of bearing steel 100Cr6 (1.3505) but also of normal steel or aluminum. We have also received inquiries for and ordered bearing housings, into which bearing pairs manufactured by us are then inserted. By outsourcing parts to Spanflug, we are also creating capacity for our in-house production.
What was your experience with Spanflug during the inquiry and ordering process?
We have been a customer of Spanflug since the very beginning. The RFQ and ordering process is simple and clear. The software is easy to use. We have already requested and ordered parts directly from Spanflug as part of project inquiries without using the platform. The process here was just as streamlined as in the software solution.
Compared to the conventional process, does Spanflug reduce your workload when purchasing parts, from the price inquiry to order processing? If so, to what extent?
Spanflug takes a lot of pressure off us compared to the conventional process. The simple uploading of parts and the fast graduated price calculation help significantly with the calculation of larger projects. This also enables us to provide our customers with a quote for our products more quickly.
Without further assistance and in a short time, we receive prices and delivery times for the required parts and can also compare them with the costs of in-house production, which we could map for some parts. However, the route via Spanflug often proves to be simpler and more cost-effective. The subsequent ordering process is completed just as quickly.
Have you so far only requested instant prices via the Spanflug platform or have you already placed project inquiries directly with the sales team?
We have parts for which there was a need for coordination, as we initially manufactured them in-house, but it then proved to be more economical to purchase them from Spanflug. Here we use the direct contact with the Spanflug employees, who support us with their machining experience. It is also very helpful that we can request samples of larger orders for approval. This allows us to minimize any errors. If reworking is necessary - we had a case where our drawing was unfortunately not clear - this process also worked perfectly.